After countless resources spent on R&D, years of engineering and processing through a multi-million dollar manufacturing plant, your product stands finished and ready for packaging at the end of the assembly line. It only stands to reason that we would package and transport such precious cargo in the industry’s most reliable material: paper.
While it may defy logic, over more than 100 years, corrugated packaging has grown to become an unwavering mainstay in the packaging industry.
How is it that an amalgam of new and recycled wood pulp is the go-to standard for packaging everything from craft beer to precision-engineered automotive components? Let’s break it down.
Why We Use Corrugated
Lightweight Durability
Corrugated packaging, while incredibly strong, is also surprisingly light. Thinking back to your high school biology class: birds are able to fly due to pockets of air in their bones that make them incredibly light for their size. The flutes running through corrugated packaging have a similar effect, reducing the weight of the materials compared to a completely solid piece of packaging. We test our corrugated boxes to ensure durability, which we talk about in more detail in our upcoming post about Box Manufacturers Certificates.
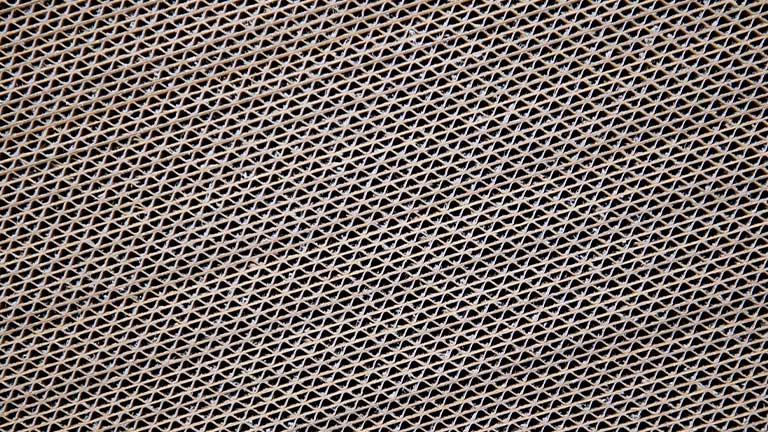
Environmentally Sustainable
Sustainability is a prominent issue for every business. Shipping and packaging is an easy way to incorporate more sustainable practices, especially with corrugated materials, which come from a readily-available, renewable resource. Corrugated materials can contain recycled paper, and are both recyclable and reusable.
Versatile & Customizable
As we mentioned earlier, you can get corrugated materials for a wide variety of uses: Boxes of varying sizes and styles, product-specific padding for shipping, permeated boxes that can transform into trays once they arrive at a store, in-box partitions and more. All of these materials and more are customizable to accommodate your exact specifications to encase, support and transport your product without sustaining undue damage.
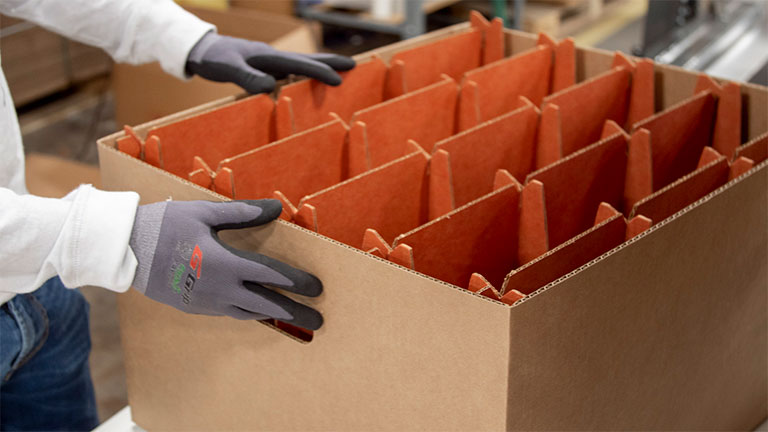
Space-Efficient
The stackability of corrugated boxes is only part of the story when we’re talking about their space-efficiency. Beyond their easily-stacked shape, our designers and engineers can help you determine the best way to transport your product. You’ll be able to move the greatest amount of product in the smallest possible space while systematically reducing the risk of damage. You can also reduce the necessary storage space for corrugated materials in your facility; most materials can be stored completely flat, allowing you to utilize precious storage space for other important materials and components.
Promotional
Especially for B2C businesses, having memorable, on-brand shipping packaging can be a vital component of your marketing strategy. Think about how you can spot an Amazon box on a front porch before you even pull into your driveway. Just seeing that logo triggers a cascade of chemicals in our brains that fill us with excitement and anticipation. We’re about to get something.
With corrugated, you can easily print customized shipping materials that will fill your clients and customers with those same emotions.
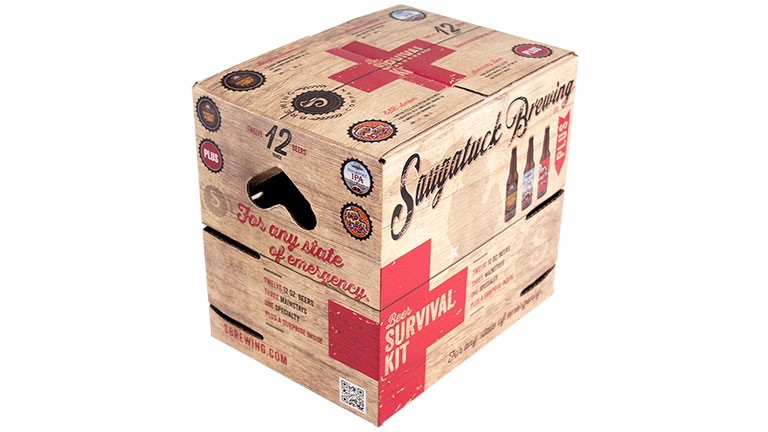
Cost-Effective
Corrugated packaging materials are the perfect example of the expression “bang for your buck.” It’s less expensive to produce (therefore cheaper to buy than other materials), easy to fill, and lightweight to reduce shipping costs. Plus, it serves multiple purposes: in many cases, you can ship, store, and set products out in a store in the same piece of packaging.
If you have any other questions about corrugated shipping or packing materials, talk with the experts! We’ve got all the answers to your questions.
What is Corrugated?
Developed in the mid nineteenth century England to reinforce tall hats, companies produce and ship an estimated 400 billion square feet of corrugated in the US alone.
Also called “fluted paper,” corrugated includes several protective paper materials with alternating layers of flat and wavy, or “crinkled,” paper. Often mistakenly called “cardboard,” corrugated materials are commonly found in the form of shipping boxes, padding, trays, partitions and more.
Anatomy of Corrugated Material
Corrugated fiberboard has two main components: the flat part, called linerboard, and the wavy part, called the medium. Containerboard, a thicker specialty paper designed for corrugated packaging, comprises both the linerboard and the medium.
When attached to the linerboard with an adhesive, the medium at the core of the corrugated packaging is able to resist bending, crushing, compression and pressure from all directions. This provides greater stability and shock absorption. Depending on the necessary strength of the box, we use different containerboard types and layering techniques.
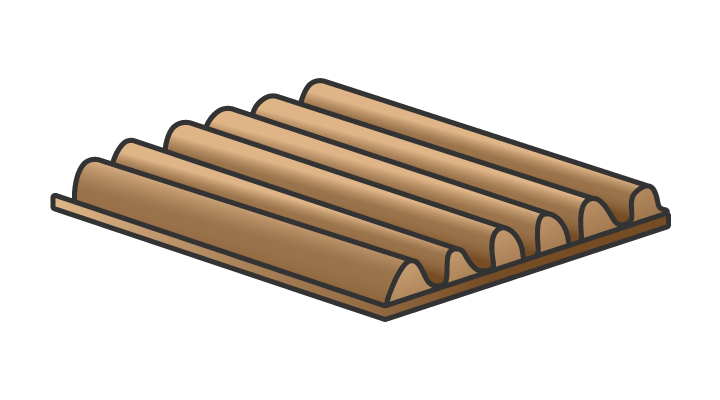
Single Face
One corrugated medium is glued to one flat sheet of linerboard; flutes exposed.
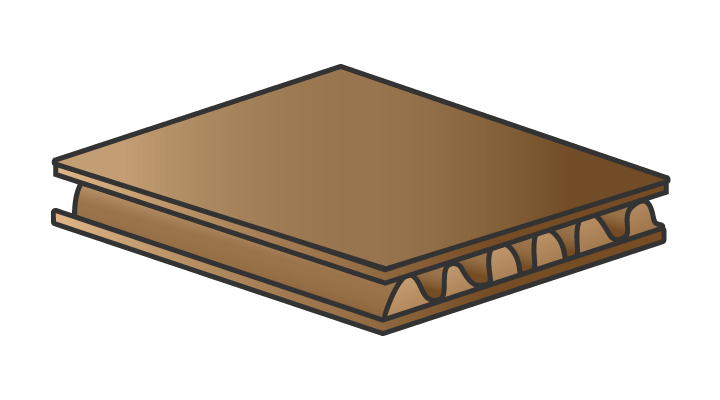
Single Wall
The corrugated medium is glued between two sheets of linerboard. Also known as doubleface.
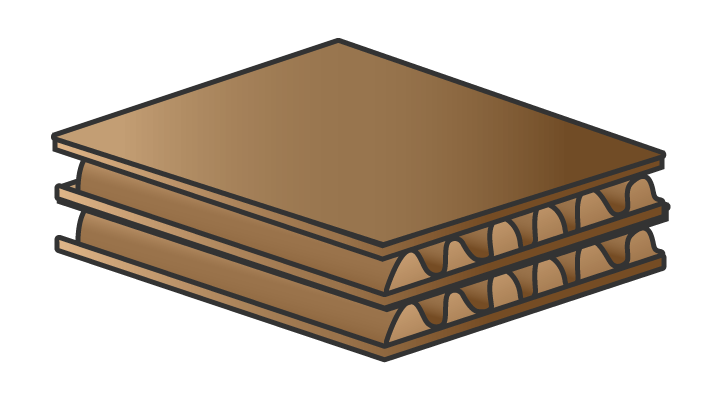
Double Wall
Three sheets of linerboard with two mediums in between.
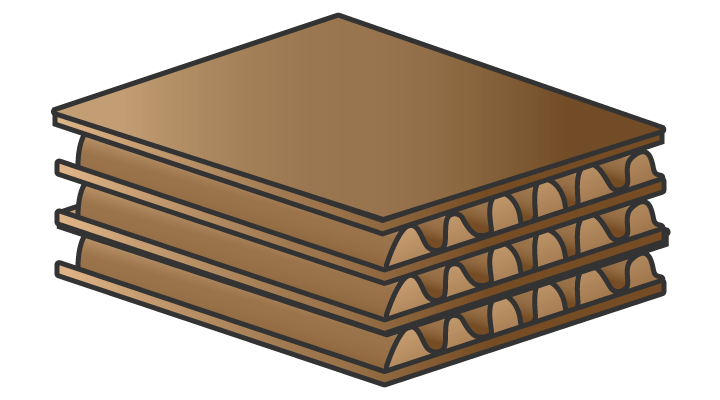
Triple Wall
Four sheets of linerboard with three mediums in between.
Flute Classifications
In the case of corrugated materials, a “flute” doesn’t refer to the high-pitched wind instrument! Imagine you have a wavy piece of medium sandwiched between two flat pieces of linerboard. If you look at that piece from the side, you’ll see little channels, sort of like tubes running through the piece of corrugated material. The waves that create those small channels are what we refer to as flutes.
Depending on what you need the corrugated packaging to do, you might need flutes spaced out thinner or wider, as well as taller or shorter. When we space flutes out wider, there will be fewer in one foot of packaging. If the flutes are more tightly packed together, there will be more. We classify corrugated packaging by how many waves there are in one foot of packaging. We refer to this number as the flute density.
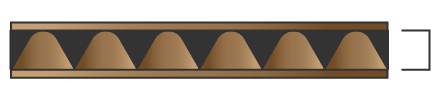
F Flute: 1/32″
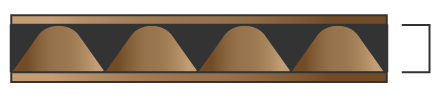
E Flute: 1/16″
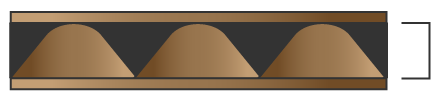
C Flute: 5/32″
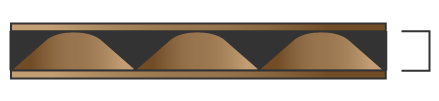
B Flute: 1/8″
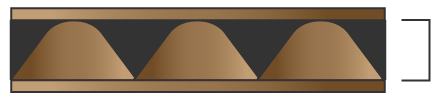
A Flute: 1/4″
Flute designation | Flutes per foot | Flute thickness (in) | Flutes per meter | Flute thickness (mm) |
---|---|---|---|---|
A flute | 33 ± 3 | 3⁄16 | 108 ± 10 | 4.8 |
B flute | 47 ± 3 | 1⁄8 | 154 ± 10 | 3.2 |
C flute | 39 ± 3 | 5⁄32 | 128 ± 10 | 4.0 |
E flute | 90 ± 4 | 1⁄16 | 295 ± 13 | 1.6 |
F flute | 125 ± 4 | 1⁄32 | 420 ± 13 | 0.8 |
A-flute was the original flute profile, and it’s still the classification with the widest flutes with a density of 33 flutes per foot. C-flute is the most commonly used in packaging with a density of 39 flutes per foot. B-flute comes in next at 47 flutes per foot and is often the preferred material for digital printing due to the tighter flute pattern. E-flute has the highest number of flutes, coming in at 90 flutes per foot.
There’s also packaging that we classify as “micro flutes,” such as F and N, that provide enhanced graphic capabilities for retail applications.
Find a Corrugated Packaging Solution
Contact us today to get your project moving in the right direction.
Give us a call or request a consultation using the form to get started.
Phone: (616) 355-9800